Em qualquer indústria, as paradas de planta são momentos críticos que exigem um planejamento adequado e uma execução impecável.
Esses períodos de inatividade são essenciais para a manutenção, reparos e atualizações dos equipamentos e sistemas, garantindo que tudo funcione de forma eficiente e segura. Porém, a complexidade desses processos pode trazer consigo grandes desafios.
Neste artigo, vamos abordar os principais desafios enfrentados durante as paradas de planta e como superá-los, apresentando as melhores práticas para garantir uma execução bem-sucedida.
Você descobrirá como uma gestão planejada e bem-informada pode fazer toda a diferença na eficiência e no sucesso das suas operações industriais.
O que são paradas de planta?
Paradas de planta, também conhecidas como paradas programadas ou desativação temporária, referem-se à interrupção planejada das operações de uma planta industrial para realizar manutenção, inspeções, upgrades ou reparos.
Esses períodos de inatividade são essenciais para garantir que os equipamentos e sistemas funcionem de maneira eficiente e segura, evitando falhas inesperadas que podem resultar em custos elevados e danos aos ativos.
As paradas de planta permitem que equipes de manutenção realizem tarefas que são impossíveis durante o funcionamento normal, como a substituição de peças desgastadas, a calibração de instrumentos e a implementação de melhorias tecnológicas.
Desafios comuns em paradas de planta
Apesar de serem muito importantes para a conformidade e segurança da indústria, as paradas de planta apresentam grandes desafios a serem superados. Abaixo estão alguns dos desafios mais comuns:
1. Planejamento e coordenação ineficientes
Um dos maiores desafios durante uma parada de planta é o planejamento e a coordenação inadequados. As paradas exigem uma preparação consistente para garantir que todos os aspectos da manutenção, reparos e atualizações sejam realizados de forma organizada e dentro do prazo estabelecido.
A falta de um planejamento pode levar a atrasos significativos, aumentando o tempo de inatividade e, consequentemente, os custos associados.
Para evitar isso, é importante desenvolver um cronograma detalhado, identificar e preparar todos os recursos necessários com antecedência, e coordenar as atividades entre diferentes equipes e fornecedores.
2. Interrupção das operações normais
Durante uma parada, a interrupção das operações normais pode afetar a produção, a logística e a cadeia de suprimentos. Essa interrupção pode resultar em atrasos na entrega de produtos, perda de receita e impactos negativos na satisfação dos clientes.
Para minimizar esses efeitos, é importante implementar estratégias de mitigação, como a programação de paradas em períodos de baixa demanda e a comunicação clara com os clientes sobre possíveis atrasos. Além disso, é fundamental ter planos de contingência para gerenciar qualquer impacto inesperado.
3. Gestão de custos e orçamentos
A gestão de custos é outro desafio significativo em paradas de planta. É comum que despesas imprevistas surjam durante a execução de trabalhos, como a necessidade de peças adicionais ou serviços extras.
Esses custos inesperados podem exceder o orçamento inicial e impactar negativamente o retorno sobre o investimento.
Para controlar os custos, é preciso criar um orçamento completo e realista, monitorar continuamente as despesas durante a parada e estabelecer um fundo de contingência para cobrir quaisquer gastos imprevistos.
Os responsáveis também devem revisar e ajustar o orçamento com base em experiências anteriores, o que pode ajudar a melhorar a precisão das previsões futuras.
4. Manutenção da qualidade e conformidade
Manter a qualidade e a conformidade com normas e regulamentações durante uma parada de planta é determinante para garantir que os equipamentos e sistemas estejam operando dentro dos padrões exigidos.
A falta de atenção a esses aspectos pode resultar em problemas de desempenho, falhas operacionais e até penalidades regulatórias.
Para garantir que a qualidade e a conformidade sejam mantidas, é importante realizar inspeções rigorosas, seguir procedimentos estabelecidos e envolver especialistas qualificados em todas as etapas do processo.
Além disso, documentar todas as atividades realizadas durante a parada ajuda a assegurar que todas as regulamentações sejam cumpridas e facilita a auditoria futura.
Planejamento e preparação para paradas de planta
Para garantir que as paradas de planta ocorram sem grandes impactos na produção, aqui vai uma lista do que deve ser planejado:
- Defina claramente os objetivos da parada.
- Crie um cronograma detalhado.
- Liste todos os recursos necessários.
- Coordene com fornecedores e equipes.
- Realize uma análise de risco.
- Prepare a documentação necessária.
- Forneça treinamento para a equipe.
- Comunique-se com todos os stakeholders.
- Faça uma inspeção preliminar.
- Realize testes simulados.
Com uma abordagem estruturada, você garante que todos os recursos e equipes estejam alinhados, que todos os riscos sejam identificados e mitigados, e que a planta retome suas operações com segurança e eficácia.
Manutenção preventiva vs. corretiva na parada de planta
Na gestão de uma planta industrial, as estratégias de manutenção impactam diretamente na eficiência e na redução dos custos operacionais.
Dois conceitos fundamentais que influenciam as paradas de planta são a manutenção preventiva e a manutenção corretiva. Compreender suas diferenças pode fazer toda a diferença no sucesso da sua operação.
Manutenção preventiva é realizada com o objetivo de evitar falhas antes que elas ocorram. Envolve inspeções regulares, ajustes e substituições programadas de componentes, baseadas em intervalos de tempo ou uso.
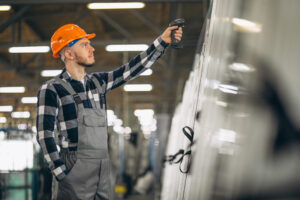
Essa abordagem reduz a probabilidade de quebras inesperadas e permite um planejamento mais eficiente das paradas de planta. Como resultado, a manutenção preventiva pode minimizar o tempo de inatividade e os custos associados às emergências, garantindo que os equipamentos estejam sempre operacionais e em boas condições.
Manutenção corretiva, por outro lado, é realizada após a ocorrência de uma falha ou avaria. Essa abordagem reativa pode levar a paradas inesperadas e não planejadas, que frequentemente resultam em tempos de inatividade mais longos e custos mais altos.
Além disso, a manutenção corretiva pode causar impactos negativos na produção e na segurança, uma vez que os problemas não são detectados e resolvidos até que se tornem críticos.
Optar por uma estratégia de manutenção preventiva pode transformar a gestão das paradas de planta, permitindo que elas sejam mais previsíveis e controláveis.
Garanta o sucesso da sua operação com a Smycotech!
A Smycotech oferece soluções especializadas para planejamento e execução de paradas de planta. Nossa equipe é formada por especialistas que entendem profundamente os desafios e as necessidades de cada cliente, assegurando que cada manutenção seja realizada com máxima eficiência e mínima interrupção.
Escolha a Smycotech e aproveite nosso conhecimento especializado para solucionar os desafios do seu negócio. Entre em contato conosco e descubra como podemos ajudar!